There are no shortcuts to making good Ductile iron pipe (DI pipe). Built upon fundamentals and protocols developed by the American Society for Testing and Materials (ASTM) and the American National Standards Institute (ANSI) came the American Water Works Association standards (AWWA), which govern and judge the consensus fitness of products as produced. These standards strictly govern the dimensions and properties of DI pipe. What separates DI pipe manufacturers is their adherence to these standards and consistent dedication to quality assurance.

1 - Have a Good "Game Plan"
"There are only so many hours in a day." We've all heard that expression through the years, hoping to make the most of each hour and every day. In that same aspect, manufacturing facilities, absent continual capital improvements or expansion, operate within similar restrictions. There's only so much product you can make in a year.
For Ductile iron pipe plants, this ultimate annual capacity is derived from the number of casting machines used across a given time, the sizes each can produce, and the diameter mix assigned across the 5 to 7 machines in use at each facility. Based on the diameter and wall class of pipe being produced, pieces made from a single machine can range from as few as 9 or 10 per hour to 50 or more per hour.
This mechanical capacity and the capability to melt enough raw materials to feed these machines during operational hours smoothly determine the efficiency of each producing plant. The "machine hours" required to meet the marketplace demand, whether daily, weekly, or annual, are constantly examined and updated as needed by facility managers and planners.
The contribution of proper production planning cannot be overstated. Production scheduling involves careful consideration of historical inventory trends, current order backlogs, customer demands, and other reliable indicators such as recent bidding trends, qualified construction forecasts, and the like. Just like with a successful football team, a good game plan is key.
Yet even with a plan, audibles are sometimes needed. This also happens in foundries when it comes to making Ductile iron pipe. A change in the pipe diameter produced by a machine already in operation requires a temporary yet complete shutdown of that line, often for hours. Far more complicated and detrimental to efficiencies than just yelling "Omaha" at the line of scrimmage!
2 - Start with "Good Dough"
If you want good cookies, start with good dough. Even the best oven in the world can't fix lousy dough! The same goes for Ductile iron pipe—metallurgy matters. The longest and most critically formative portion of the DI pipe-making process is the hour-plus slow-roll trip through the annealing oven at temperatures ranging from 1900°F upon entry to just above 1300°F at the exit. Every other step in the process occurs in generally less than a minute.
But suppose the mix of materials and reagents is not correct at the start, just like cookies. In that case, the annealing oven cannot fix it, and the resultant metal chemistry and nodularity are likely to be "less than Ductile." True and lasting quality begins in the raw material mix and melting.
Ductile iron pipe is made from nearly 95% post-consumer and light-industrial RECYCLED materials, primarily shredded automobiles. Engine blocks, brake rotors, metallic frames, and other recycled structural plates and steel are the preferred components of this mix. If you look at the pile of scrap at the plant, one can often identify such recycled materials.
This "major ingredient" of Ductile iron pipe is a commodity-grade mix whose cost fluctuates with the worldwide open market conditions. Makers of Ductile iron pipe avoid copper, chrome, nickel, and tin, and other undesired elements being in this mix as those – even in relatively small amounts – can spoil the "dough."
Specific alloys and raw coke are added to batches of scrap material prior to deposit in the cupola, where the melting occurs in a highly controlled and continually monitored water-cooled procedure. The coke serves as a primary fuel for the melt. Each 8 to 10-ton batch of melted metal is tested for consistency towards the intent and need as a base sample. Just like tasting the sauce before you add it to the pasta! It's too late afterward if you don't.
Conversion to the nodular ferritic structure of Ductile iron then begins by introducing a measured amount of solid magnesium into each batch, inducing the desired iron chemistry. You now have approximately 20-minutes to make pipe from this small batch of iron before it gets too cold to use. The molten iron temperature at the casting machine pour is approximately 2500°F.
3 - Be Good to People and the Environment
For most of the 20th century, foundry work, including making cast iron pipes - both gray and Ductile - was tough, dirty work. While improvements were gradual and welcomed in the 1990s, the true Environmental Heath & Safety (EHS) breakthroughs began in 2003, many spearheaded by McWane Ductile. The work is still challenging, yet it is now magnitudes safer for workers and consciously friendly to the environment and end-users.
Solvent-based asphaltic paint, known as sealcoat, was replaced by modern water-based versions of the same beginning in 2003. These new asphaltic paints effectively contain no volatile organic compounds (VOCs). With none in, none can depart and foul the transported water. These water-based sealcoats also dry quicker and afford easy clean-up in the foundry without the need for additional chemical cleansers. That’s people-friendly, from start to finish.
With many industrial manufacturing facilities, emissions have always been a source of concern and debate. In 2005, McWane Ductile installed the first mercury emission capture baghouse in the domestic Ductile iron industry at their Phillipsburg, New Jersey location. This was a significant capital investment towards improved environmental interaction. Because of its success, McWane repeated it at other foundries.
While these baghouses minimize and “scrub” exhausts from the foundry, their primary function is to eliminate potentially dangerous elements from escaping the melting process. Mercury is contained, albeit in small amounts, in some electrical components and parts of an automobile, such as circuit boards. Captured impurities are properly deposited at appropriately registered landfills.
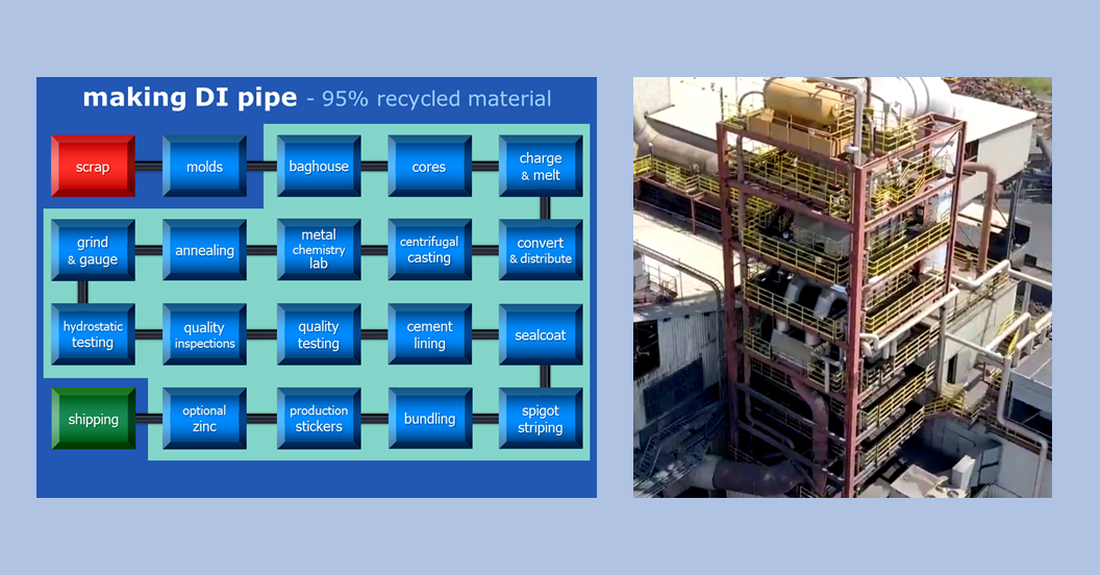
Additionally, the stormwater drainage systems of all McWane Ductile properties are purposely separated from contributing to the community collection system. Whether it’s rainwater runoff or our own water used in the production, all is captured and treated through on-property water treatment facilities. This process allows the treated water to be reused in subsequent pipe manufacturing, which also reduces the draw of new water from community supply sources.
The Occupational Safety and Health Administration (OSHA) has a specialized program and recognition for companies that have demonstrated and documented a substantial commitment to superior safety protocols and operations. Known as the Voluntary Protection Program (VPP), McWane Ductile has been accredited with Star Status at its three pipe-producing facilities, with the highest level of recognition in the OSHA program. Over time, the work required to achieve this status has fundamentally and significantly improved the safety culture at all facilities. It's a true source of pride to know you're making pipe safer and cleaner than most, if not all, others.
4 - Apply Consistent Quality Assurance
Most of the decisions and actions taken within a DI pipe plant during production remain in constant accordance with the dimension and material properties mandated by applicable AWWA standards, with testing performed at a rate "random enough to ensure compliance ."
Most producers test at a rate more frequent than minimally required, understanding that a primary separator of one plant or manufacturer from another is the dedication to "eyes on the prize," i.e., Quality Assurance inspections and testing throughout the process. Visual examinations, comprehensive dimensional checks, metal sampling, some destructive testing, and more – it’s all about ensuring product consistency and the minimum 100-year service life expected from Ductile iron pipe and fittings
5 - Test Every Pipe Individually Beyond Its Service Needs
The one test of Ductile iron pipe in all foundries that is performed on every single piece of pipe produced, 100%, no exceptions, is the hydrostatic pressure test. Every DI pipe, before it proceeds into the finishing process, where it receives a lining and/or sealcoat, undergoes a filling and positive containment exam by 500-psi of internal water pressure.
Any minor insufficiency that other exams might not catch from human inspectors is surely to be discovered by the stress of holding 500-psi inside. It's nice to know that every DI pipe you receive has already proved itself against more than 4-times the average system working pressure to be experienced in service, surges included.
6 - Support Your Pipes for a Lifetime
Another source of pride and/or separation of one producer from another is their demonstrated dedication to hands-on support and services provided after the sale. Whether assisting from afar or handling emergent issues onsite, McWane ductile has a team of highly qualified personnel ready to help, at no cost to you, whenever and wherever needed.If it's made by McWane, it will be supported by McWane, always. Our integrity and support are never-ending.
Summary
DI pipe is a long round metal tube with empty space down the middle…how hard can it be to produce? You'd be surprised. Arrange a plant tour at any of McWane Ductile or other pipe-producing facilities, and you will be surprised how much design, thought, planning, and stringent control goes into it. If nothing else, you will emerge with a greater appreciation for your day job, guaranteed. Contact your local Sales Representative or Distributor Supply House to arrange a plant visit and appreciate what it takes!