A Project to Remember
Over the course of my 30+ year career with McWane Ductile, I’ve had the opportunity to be a part of some remarkably interesting and detailed water pipeline projects. Several of these projects have required a partnership between the community, awarding authority, contractor, water works distributor, and material manufacturer to ensure the projects were installed efficiently and correctly. However, few have matched the scale, complexity, and collaborative effort of the Saugus River crossing—part of the massive Belden G. Bly Bridge Replacement Project in Massachusetts. This project stands out not only for its technical challenges but also for the preparation, planning, and collaboration of key partners that brought it to a successful conclusion. In this #IronStrong Blog, you’ll hear the when, why, who, and how of this complex and intricate Ductile iron pipe (DI pipe) waterway crossing.
Project Location and Scope
The project was centered around the Route 107 (Salem Turnpike/Western Avenue) bridge that spans the Saugus River, connecting the communities of Lynn and Saugus, Massachusetts. The Massachusetts Department of Transportation (MassDOT) awarded a contract worth $84+ million to the successful bidder, SPS New England (SPS) of Salisbury, for the complete replacement of the Belden G. Bly Bridge. This included the construction of a temporary bridge and pedestrian walkway, removing the existing bridge, and installing a Dutch-style bascule bridge—something rarely seen in the United States.
As part of this extensive infrastructure overhaul, the project included roadway and drainage improvements along Route 107 in Lynn and Saugus, MA, and Ballard Street in Saugus. The Massachusetts Water Resources Authority (MWRA) required a waterline interconnection between Saugus and Lynn to be installed directly beneath the Saugus River.
Why the Project Was Needed
This interconnection was essential to modernize and strengthen the water distribution system for both communities. Ensuring reliable water service across this critical river crossing would help future-proof the area’s infrastructure and allow for operational flexibility between towns.
Who Was Involved
The project brought together a powerful team. SPS New England, based in Salisbury, MA, was the prime contractor. F.W. Webb Company (F.W. Webb) of Malden, MA served as the waterworks distributor. From our side, McWane Ductile supported the effort with engineering guidance, materials expertise, and on-site coordination.
Project planning began in earnest with a preconstruction discovery meeting in March 2022, where I joined National Product Engineer Ken Rickvalsky and other key personnel from SPS New England to better understand the project requirements, walk the site, review the drawings, and assess field conditions. Once observed, we offered insight into potential installation methods based on the specified material. It was also determined that there may be an opportunity to provide an alternative pipeline configuration to satisfy the crossing requirements.
-
L to R: Jimmy Waugh, Sales Rep, F.W. Webb; Jack Pecora, Executive Project Manager, SPS New England; Jeff Houser, Senior Sales Rep, McWane Ductile. -
Belden Bly Bridge Replacement job site signage. -
From L to R: McWane Ductile's Cory Humphreys, Technical Specialist and Ken Rickvalsky, National Product Engineer.
Material Selection and Why Ductile Iron Was Chosen
After thorough discussions, McWane Ductile’s Technical Services Specialist, Cory Humphreys, was called upon to review the existing drawings and offer other product solutions. Cory went to the drawing board (literally) and produced two alternative configurations, including a detailed lay schedule and bill of materials required to connect Saugus to Lynn successfully. One of these was approved in early 2023, and production was scheduled.
The final design called for Ductile iron pipeline (DI pipe) materials:
- 576 feet of 16-inch and 342 feet of 20-inch TR Flex® Boltless Push-On Restrained Joint Pipe
- 54 feet of 20-inch Mechanical Joint (MJ) Pipe
- All pipes were Class 52, cement-lined inside, zinc-coated with a seal coat exterior, and wrapped with V-Bio® Enhanced Polyethylene Encasement.
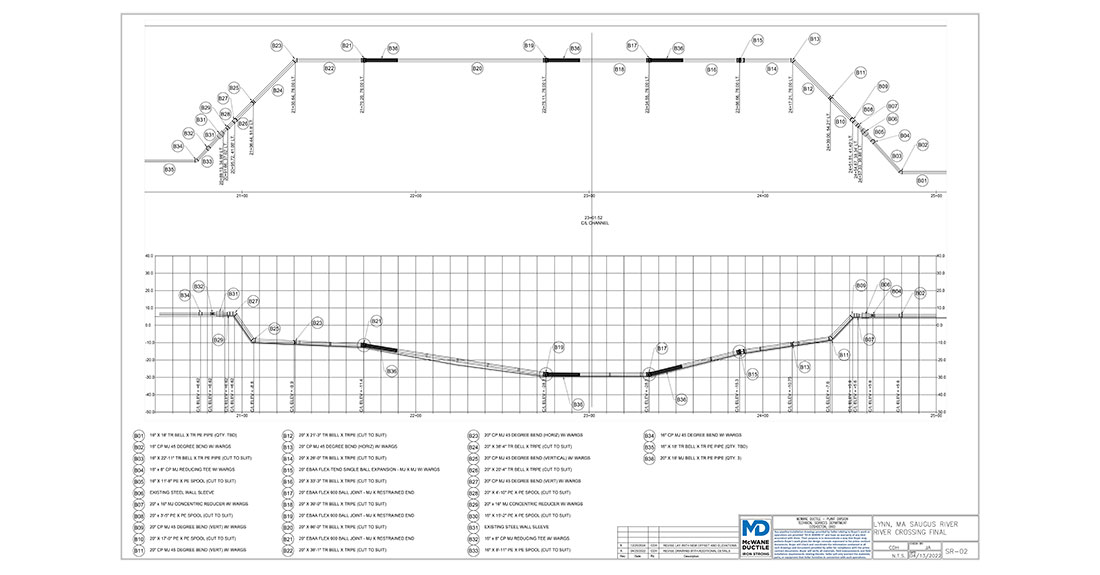
In early January 2023, once an alternative was refined, selected, and approved, SPS NE, F.W. Webb, and McWane Ductile came together and put this project on the books for manufacturing. During this timeframe, some Ductile iron pipe manufacturers had a sizeable backlog arising from the COVID-19 pandemic and supply chain issues, so it was fortunate that ample time was allotted prior to installation. Once the product had been manufactured and finished, the pipe was delivered to the site for future installation.
A ductile iron pipe was selected because of its strength, long-term performance, and ability to withstand extreme environmental conditions—which are critical factors for a submerged installation in a tidal, freezing environment. Alternative materials simply couldn’t offer the same resilience or durability in the face of sub-zero temperatures, tidal shifts, and underwater placement.
Construction Process
By late 2024, SPS’s bridge construction progress allowed SPS to target early 2025 for the pipe installation. In mid-December, another preconstruction meeting brought our team together with SPS and F.W. Webb to finalize logistics and procedures. I personally reviewed the material staging area and noticed a missing weldment on the Mechanical Joint pipe needed for the TR Flex transition. Thanks to quick communication with Cory Humphreys and our plant in Ohio, the issue was corrected without delaying the timeline.
Come January 2025, the final push began. Ken, Cory, and I were back on-site with the SPS crew to pre-assemble the pipe sections per the detailed lay schedule. The Saugus River, an active waterway for local fishermen, required a temporary closure approval from the Coast Guard. SPS had to plan around high tide windows and work in biting cold—single-digit temperatures and wind chills that stung through multiple layers.
SPS assembled and floated the 16- and 20-inch pipes out into the channel, adjacent to pre-installed sheeting. A barge-mounted Caterpillar 336F with Trimble GPS was used to dredge a trench 4 feet below the mud line. This trench would cradle the waterline once sunk into place.
Final Installation: Teamwork in Action
Originally, SPS aimed to complete the crossing the week of January 20, but extreme cold and dangerous wind gusts forced a delay. SPS crew regrouped and rescheduled for the week of January 27. On the 28th, the big day arrived.
The SPS team was ready. Two heavy-lift cranes—one 150-ton American Crane and one 110-ton Liebherr Crane—were stationed on each side of the river. Bridles supported the connection risers, and a water truck was on hand to help fill the pipeline gradually, overcoming its buoyancy. Marine personnel, Black Dog Divers, and GPS verification equipment ensured the pipe settled precisely in the trench.
With risers in place and both ends aligned for connection to the municipal water system, the team choreographed a successful and safe submersion of the waterline. It was a long day but an immensely satisfying one.
-
A barge-mounted excavator dredged a trench in the river bed using GPS. -
High-capacity cranes hoisted the connection risers on each side of the riverbank. -
Marine crews attached the risers with DI bends at each end. -
A water truck filled the pipeline to overcome buoyancy. Divers guided the pipe to the bottom.
Conclusion: Success Through Collaboration
The Saugus River crossing project was a masterclass in coordination. From design and engineering to manufacturing and field installation, every party played a crucial role. I’m proud of how we, along with SPS New England, F.W. Webb, and my colleagues at McWane Ductile, collaborated under pressure and in extreme conditions to deliver a top-tier solution.
On March 7, 2025, we reached the final milestone: the new pipeline passed a 150-psi hydrostatic test on the first attempt in accordance with AWWA C600 standards. That moment confirmed what we all knew—this project was built to last.
Need Assistance with Your Waterworks Project?
If you have any questions regarding your water or wastewater infrastructure project, your local McWane Ductile representative is equipped with the expertise to assist you. Many of our team members have managed small and large water utility systems, served in engineering consulting firms, and bring decades of experience solving field issues involving pipeline construction and operation. From design to submittal to installation, we strive to educate and assist water professionals throughout the water and wastewater industry.