Welcome to our Halloween edition of #IronStrong," where we’ve compiled the spooky challenges haunting construction builders and pipeline contractors. From tricky terrain to mysterious leaks and unforeseen obstacles, we’re here to illuminate the “scary” aspects of water pipeline installations that can send chills down any project manager's spine.
See the “Ditch Doctor” advice column and a link to another blog on "Exorcising Restraint." We dissect a few daunting issues and present real-world solutions and insights to help brave contractors turn their nightmares into success stories. Grab your flashlight (and tools) as we guide you through the shadows, ensuring your next project is well-prepared to face any “frightening” twist that may lie ahead.
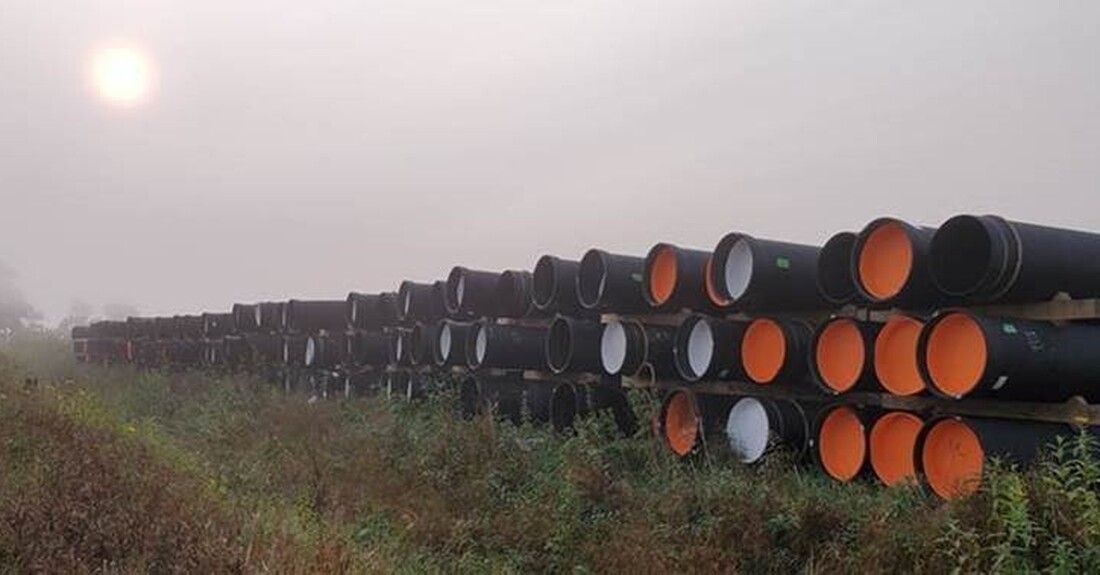
DEAR DITCH DOCTOR,
It’s Halloween out here in a spooky-named town, and this job I’m on is truly bewitching me! The supervising engineer for the project now tells me the “grippy gaskets” (you know, those ones with the metal teeth in them) are not as good as “real restrained joints,” and he won’t allow their use in this pipeline. Our main issue is that those gaskets are already on site, and we are running out of time. Tight deadlines and tough inspections are really creating a nightmare for me out here. Any tricks or treats you can offer? Help me!
Sincerely,
Freaking Out in Frankenstein, MO
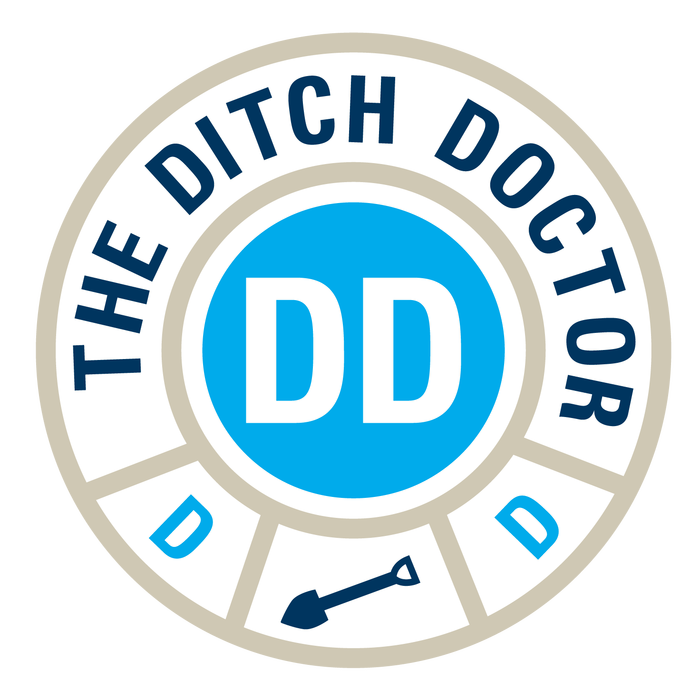
DEAR FREAKING OUT
Isn’t construction fun? OK, now that you’ve stopped screaming at my first thought, let me help you out. As your Ditch Doctor, I have no tricks or treats today … just facts! To begin with, “those gaskets with the metal teeth in them” are real restrained joints! In fact, in terms of holding a joint together with nothing other than “the power of those teeth,” these gaskets are the general performance equivalent of any as-cast and fabricated “real restrained joint.”
Both types of restrained joints are typically rated to 350 psi, which means (with safety factors involved) this provides lasting joint stability at levels of anywhere from 700 psi to 900 psi of actual internal fluid pressure, depending upon pipe diameter. That sounds very REAL to me, and I’m sure you and he would agree. In fact, the primary instance in which fabricated restrained joints are superior is when excessive end-pull forces are involved, such as in horizontal directional drilling installations or long pipelines on steep or vertical alignments. The end-pull rating for fabricated restrained joints is often 25% greater or more than “gaskets with teeth,” and fabricated joints adapt better to the sometimes-twisting forces of these installations. “Gaskets with teeth” are also not recommended for installations where repetitive vibrations or oscillation, such as on bridges, can be anticipated.
On the bright side, however, there is no waiting on foundry fabrication or delivery schedules for the vast array of standard and buried installation scenarios when using “gaskets with teeth.” Simply place a “restraining gasket” (ours are called Sure Stop 350™) into the bell of any Tyton® joint pipe. Your previously unrestrained Ductile iron pipe is instantly transformed into a quickly and reliably installed FULLY RESTRAINED PIPE FOR LIFE! I would be glad to meet with you and the engineer in question if more information or discussion is needed.
Keep Your Grip this Halloween!
The Ditch Doctor
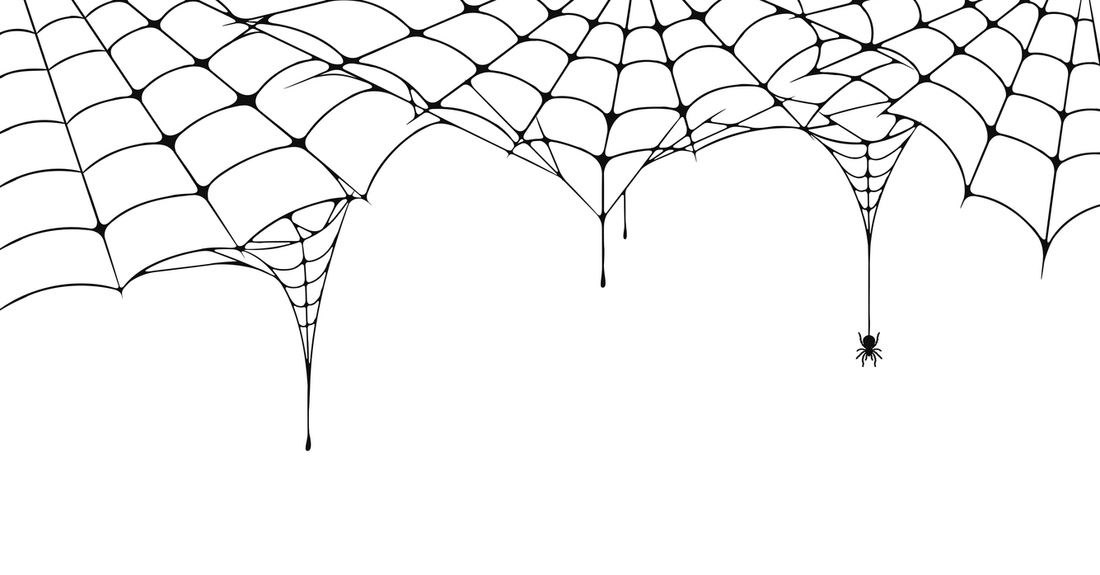
DEAR DITCH DOCTOR,
Out here in the western United States, we wind up with a lot of pipelines installed up or down serious hills, dare I say mountains as well? We are good at the construction part, yet time after time, we struggle to get a satisfactory post-installation hydrostatic test on the pipeline, especially with inclined installations. Often, the pipeline drops anywhere from 20 to 50 psi on the gauge, and we can do that several times or more until we take some sort of drastic redo/restart of the test procedures. Rarely is there ever a true leak involved; we just seem to “battle the gauge” with repetitive pumping, draining, refilling, blow-offs, and other stuff until somehow — wham! — it passes. Often the pipeline drops anywhere from 20 to 50 psi, far more than the 5 psi allowed by the AWWA standards, so we never even get the opportunity to check for “recovery allowance,” i.e., part 2 of the AWWA hydrotest. Is there a TRICK I’m missing, or is it just that TREATS don’t exist in this line of work?
Sincerely,
Vanquished in Vancouver, WA
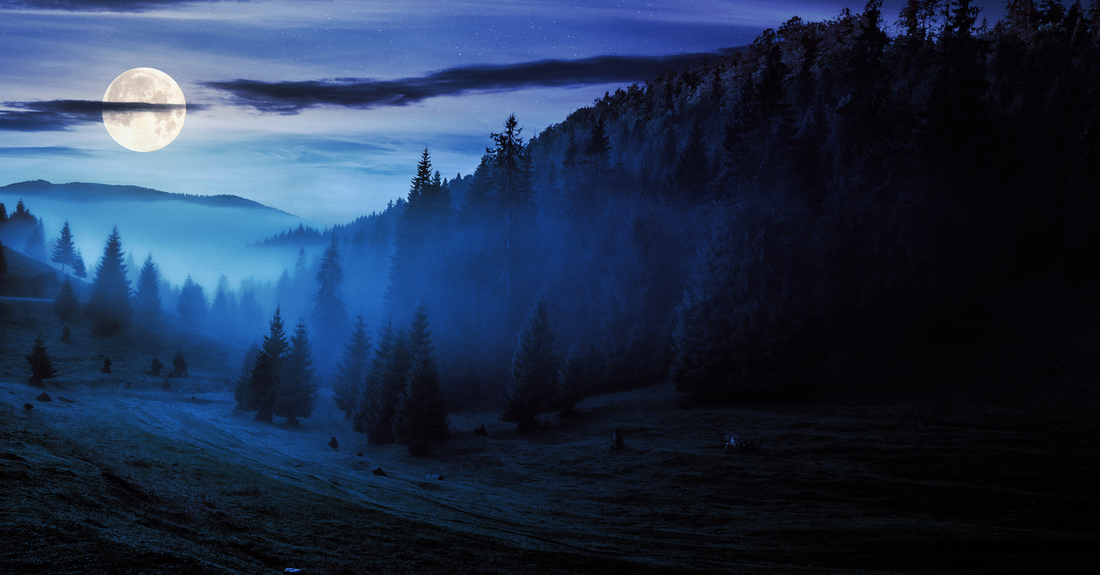
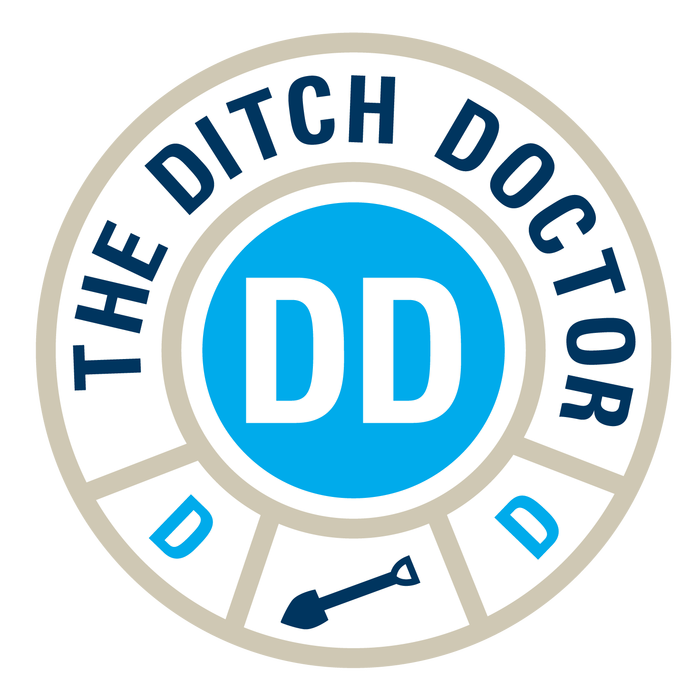
DEAR VANQUISHED,
I am glad to hear of your experienced confidence in constructing things! Let me try to help you with things you’re suffering past that. The first rule of success in hydrostatic testing of Ductile iron pipelines is operating in strict adherence to a few basic rules:
- Fill from the lowest point and bleed air from the highest point. Not close to each, but at each location.
- Fill slow, and let it blow. Filling too fast (turbulent flow) or not having an appropriately sized air-release mechanism at the high end virtually guarantees you will trap air pockets within the pipeline, even if it’s laid “flat and straight.”
- Never fill from the high side. That is a guaranteed air-trapping invite and often creates hardships far beyond the norm we’d have to cover in a different discussion.
- Losing more than 5 psi is not the end of it all. While this would disqualify you from “passing the test,” it offers you no insight as to what’s really going on. For that you need to go diagnostic, and there’s an easy way to do that. A simple Google search for “Hydrostatic Diagnostic” will put you on the right path. You’ll even find a handy tip sheet and data tracking form there.
- Lastly, and certainly on all inclined installations, placing a pressure gauge at both the low point (from where you’re pumping) and the high point (where you’re blowing air out of the pipeline) is wildly helpful.
By knowing the relationship between a water column vs. pressure created (0.433 psi per vertical foot of water), you can compare the pressure values at the top and bottom to gauge if the pipeline is hydraulically tight despite the pressure drop experienced. Much like a balloon will not stay inflated if it has even a microscopic pinhole, or a thermometer won’t stay red if there’s a hole in the tube, a pipeline with a true leak — especially an inclined one — will typically drop to zero pressure in as short a period as an overnight sit. If it stays at, let’s say, 64 psi overnight, then at least we know there’s no need to check for leaks below an elevation of 148 feet above the lower gauge’s location. That part is leak-free, i.e., the red part of a thermometer doesn’t lie! So, there are a few TRICKY TREATS to help you through, reliable and proven, just like Ductile iron is made to be!
Hoping this Gets Rid of Your Ghouls ,
The Ditch Doctor
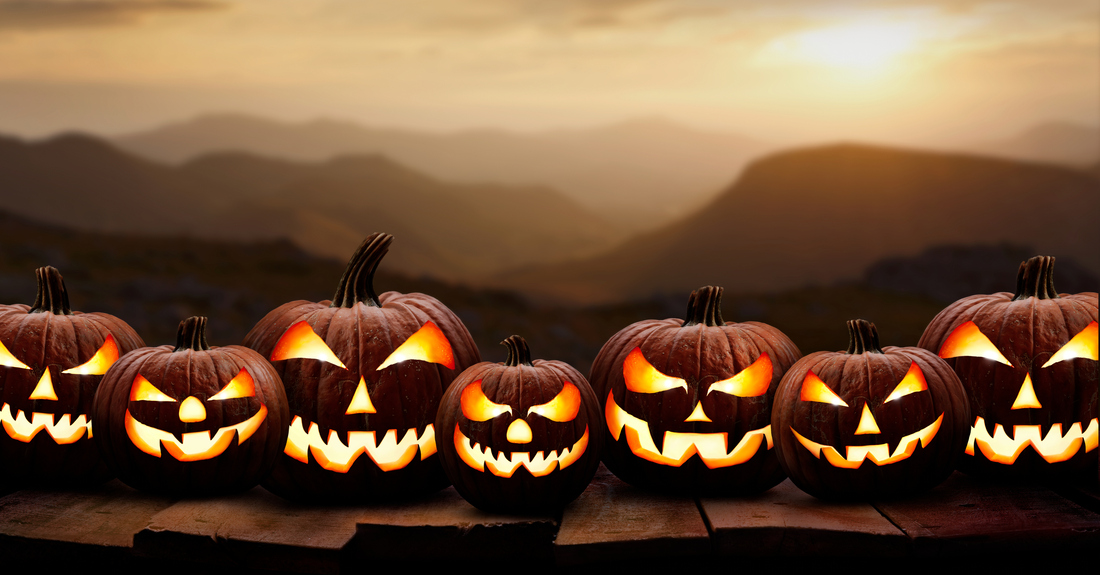
Don't Get Spooked - There's More!
And if you thought the Ditch Doctor column was interesting reading, be sure to check out this timely Halloween-themed #IronStrong blog by Ken Rickvalsky titled, “Exorcising Restraint: Deleting the Demonology,” where he delves into the why, where, and when gaskets are best suited for pipeline design and when they’re not.
We hope these stories have helped transform what may be perceived as “scary” pipeline installation challenges into manageable tasks. By sharing practical solutions, we aim to equip you with valuable tricks that go beyond the holiday and support your projects all year round. Remember, each project may come with its own set of haunting surprises, but with the right knowledge, preparation, and a little help from the Ditch Doctor, you can face them confidently.
Need Assistance with Your Waterworks Project?
Many of our team members have managed small and large water utility systems, served in engineering consulting firms, and bring decades of experience solving field issues involving pipeline construction and operation. From design to submittal to installation, we strive to educate and assist water professionals throughout the water and wastewater industry. Contact your local McWane Ductile Sales Representative today.