What is the McWane Ergo Cup?
Ergonomics is an applied science concerned with designing and arranging objects people use so that people and things interact most efficiently and safely. Reducing the risk of injury through proactive programs is one of the many ways we do our best to improve the ergonomics of the ways we make our products. At McWane Ductile and McWane corporate-wide, health and safety are the top priorities, hence the Ergo Cup.
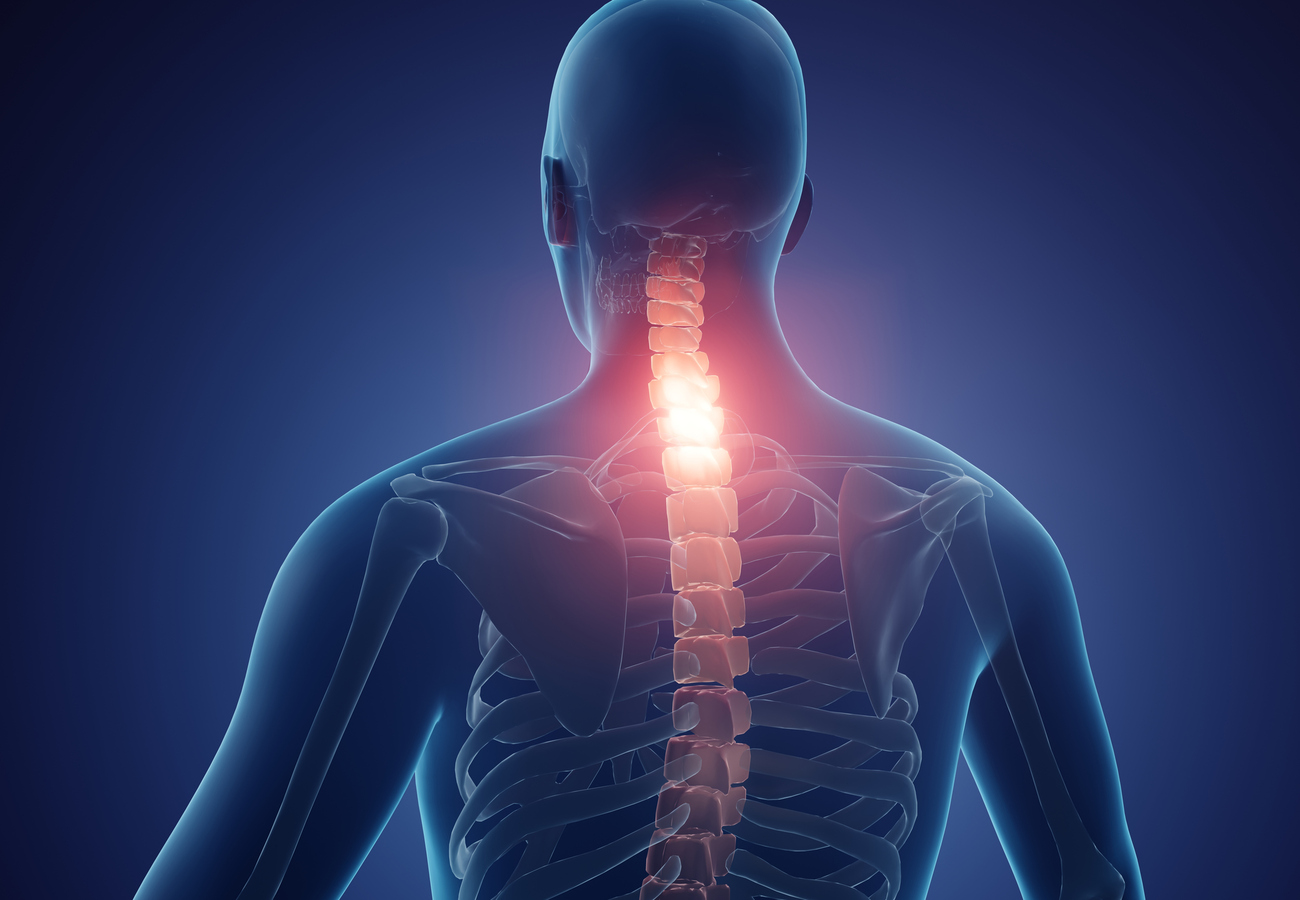
How does McWane encourage ergonomic improvements?
Each year, McWane holds an internal Ergo Cup Competition. Teams from McWane facilities around the country present ergonomic-related projects they have implemented within the last 24 months to a panel of health and safety experts.
Each project aims to reduce injuries while improving workplace efficiency and transforming processes to best suit our team members' needs. The successes of these projects are then implemented at other McWane facilities with similar operations, reducing risks company-wide. The competition winners then go on to the National Ergo Cup Competition.
How are Ergo Cup submissions selected?
From annual and monthly safety and environmental audits completed at several levels within the facility to safety committee meetings and even daily pre-shift meetings, safety is the top priority at every McWane business.
Through these audits, meetings, near-miss accident reports, and anonymous suggestions from anyone at the facility, jobs with a higher risk of injury are identified to find a safer and more ergonomic way of being performed.
Teams from several departments and different job levels are selected to evaluate tasks with a higher risk of injury. The group then devises a new way of performing the task or engineering controls to reduce the risk.
How is the risk evaluated?
Various ergonomic assessment tools are used when analyzing the potential risks of a job task. One such tool is the REBA Employee Assessment Worksheet. REBA stands for Rapid Entire Body Assessment. The REBA tool was developed to identify high-risk postures while performing work.
Data is collected on the following:
- Postures developed
- Type of movement
- Repetition
- Forces used
- Coupling
Each team member fills out the REBA form while performing an audit focused on the following:
- The job task
- Select the postures for assessment
- Score the poses
- Process the scores
- Establish the REBA score
A final REBA score is generated to indicate the level of risk and urgency with which action is recommended.

How are Ergo Cup submissions developed?
There are three project categories:
- Workplace solution I (Team driven)
- Workplace solution II (Engineering)
- Ergonomic Program Improvement Initiative
Workplace Solution (team-driven) – 75% of the problem-solving effort must be developed by employees whose primary responsibilities involve production or maintenance. Some technical support by in-house health and safety engineering staff is permitted. The team's proposal should be a newly created device or process. The solution must be simple, straightforward, and significantly reduce or eliminate ergonomic risk. The team should be able to explain the plan's financial benefits and demonstrate the company's return on investment.
Workplace Solution II (Engineering): This solution meets the same criteria as the team-driven workplace solution but allows some technical advice from outside consultants. However, in-house staff must conduct most activities.
Ergonomic Program Improvement Initiative—This must be a planned campaign, process, or management system designed to improve the effectiveness of a location's comprehensive ergonomics program.
Examples include, but are not limited to:
- Ergonomic training programs
- Incorporating ergonomics into change management systems
- Ergonomic risk assessment processes
- Ergonomic prioritization systems
- Return-to-work programs
- Office ergonomic programs designed for mobile and/or telecommuter employees.
Each company team comes up with a solution for the job task they are evaluating. The teams' solutions are then presented to a panel at the company to be approved for submittal to the McWane-wide Ergo Cup. While some ideas may not be submitted to the larger competition, all are developed to find a safer and more ergonomic-friendly way of performing the task. Ultimately, one winner is selected from the McWane-wide Ergo Cup to compete nationally.
Ergo Cup submissions applied to other companies.
Several job tasks are similar at various McWane companies despite these facilities making different products. This similarity means innovations developed during the Ergo Cup competition can be shared across the McWane family.
For instance, hoists are used at many McWane factories. Kennedy Valve submitted an Ergo Cup submission on hoist change-outs. This improvement can protect the health and safety of employees well beyond Kennedy Valve.
Ergo Cup improvements go beyond just safety.
"The commitment to safety shown by our team members, on behalf of each other and McWane, is inspiring," said Barb Wisniewski, retired Vice President of Health and Safety with McWane. "This is a perfect example of the McWane Way in action."
Ergo cup solutions go beyond improving ergonomics and reducing the risk of injury. For instance, McWane Ductile-Ohio developed an "iron chilling project." This project focused on cooling the molten iron at the machine to maintain the ideal temperature for making Ductile iron pipe (DI pipe).
The benefit of this corrective action was three-fold. First, the ideal iron temperature helps reduce defects and rejects. Second, the pipe is produced with a more consistent weight and wall thickness. Finally, there are improvements to the speed of the production line.
Another submission came from the Universal Test Facility at McWane Ductile, which evaluates product complaints. The lab occasionally receives pipes connected by a Sure Stop 350® Gasket.
Pipe with Sure Stop Gaskets still intact are very difficult to separate. The lab team devised a more ergonomic and safer way of unlocking the joint. McWane Ductile shared this solution with builders and contractors who also need to separate pipes in the field, strengthening our customer service efforts.
What is the timeline of the Ergo Cup Competition?
- January – A Formal announcement is made company-wide
- January – June
- Energize all Team Members to participate – all ideas for ergonomic improvements are welcomed
- Facilities decide on projects. Application for entries are submitted and team members begin working on projects
- September – Completed projects are to Corporate for judging by outside independent Judges. Projects are posted on SharePoint
- October 20, or before – Ergo-Cup Winners are announced
- Late October – Winning Team Completes & Submits Application for National Ergo Cup Competition
- March – National Ergo Cup Competition
From Competition Comes Innovation
The technology and process of safely manufacturing Ductile iron pipe and other waterworks products have developed significantly over the years. Even with numerous improvements, the backbone of every McWane facility is its people. Hence, there is a need to focus on ergonomics to reduce injury and increase efficiency. The McWane Ergo Cup has proven to be a friendly competition among employees and creates meaningful innovation to be shared across all McWane facilities. We're proud of the results of past competitions, as listed below, and we look forward to seeing many more ideas to come.
2022 Ergo Cup Winners
-
Most Outstanding Project: Waterman, Exeter, California - Rotary Weld Fixture
- The rotary weld fixture was designed to reduce back and shoulder pain from the movements required during the steel gate product line welding.
- 1st Place Runner Up: Clow Valve Company, Oskaloosa, Iowa - Pattern Picker
- Changing patterns for the molding machine required excessive heavy lifting, putting the brass production team at risk of back, neck, and other injuries. To solve this, the team engineered the "Pattern Picker," a motorized tool to pick up patterns from the rack and move them safely to the pattern table without manual lifting. The solution virtually eliminated the ergonomic risk to the upper extremities, lower extremities, and back while performing this task.
- Best Risk Reduction: Kennedy Valve, Elmira, New York - Hoist Change-out
- Mechanics replacing or repairing hoists in Kennedy Valve's cleaning room were at risk of injury from supporting the significant weight above shoulder level while working from a ladder. The team modified existing equipment to create a hoist lift to eliminate manual lifting when replacing hoists, thus significantly reducing the risk of ladder falls, strain or sprains to the shoulder and back, and equipment dropping that could harm other team members.
- Best Innovation Project: Amerex, Trussville, Alabama - Collar Rework
- This project removed the manual aspects of the PEX collar rework station to include a modified drill press to execute the repetitive motion as well as guards to prevent contact with the new moving machine parts.
Have Questions About the Ergo Cup, Need Assistance with Your Waterworks Project?
If you'd like to learn more about the McWane Ergo Cup or have any questions regarding your water or wastewater infrastructure project, be sure to reach out to your local McWane Ductile representative. We have team members who've managed small and large water utility systems, served in engineering consulting firms, and bring decades of experience in solving field issues involving pipeline construction and operation. From design to submittal, to installation, we strive to provide education and assistance to water professionals throughout the water and wastewater industry.