Energy resources are a big concern within our society. It is hard to listen to the news without some mention of energy. There is a finite amount available, and how we use our energy will have lasting effects on future generations. Since water and sewer infrastructure plays such a significant role in the total energy consumption of municipalities, more emphasis should be placed on energy savings when selecting pipe materials.
Engineers and utilities I interact with are familiar with designing pumps to maximum pumping efficiency, thus lowering pumping electrical costs but are typically unaware of the potential energy savings over the design life of piping materials. Many overlook the proper flow rate/hydraulic comparisons and focus mainly on the price per foot on the bid form. They ultimately pay more in the long run.

INSIDE DIAMETER – BIGGER IS BETTER
Regarding the Inside Diameter of water pipelines, Ductile iron has a significant advantage over other materials mainly because of its inherent strength. The natural strength of Ductile iron pipe (DI pipe) allows the wall thickness to be smaller compared to other materials giving DI pipe a larger inside diameter.
Bigger is better, especially when a utility looks at the monthly electric bills it pays for pumping water throughout the system. As an illustration, imagine drinking your favorite beverage with a normal size straw; it is easy to get your beverage from the cup.
Now imagine trying to take a drink of your favorite beverage with a smaller diameter coffee or stirring straw. It will take much more effort to get the beverage from the cup. Municipal pumps have similar issues when pumping through a smaller diameter. It just takes more energy to move liquid through a smaller area.

4 FACTORS THAT AFFECT WATER RESISTANCE THROUGH A PIPELINE
When water flows through a pipeline, four factors affect the resistance to that flow:
1) The velocity of the water flow
2) The roughness of the interior surface of the pipe
3) The length of the pipeline
4) The internal diameter of the pipe
When all these variables are identified, they can be placed into the well-known Hazen-Williams Formula, listed below, to determine the head loss occurring in the pipeline. Ductile iron pipe has hydraulic advantages. Because of its larger insider diameter, there is less head loss in DI pipe compared to other materials.
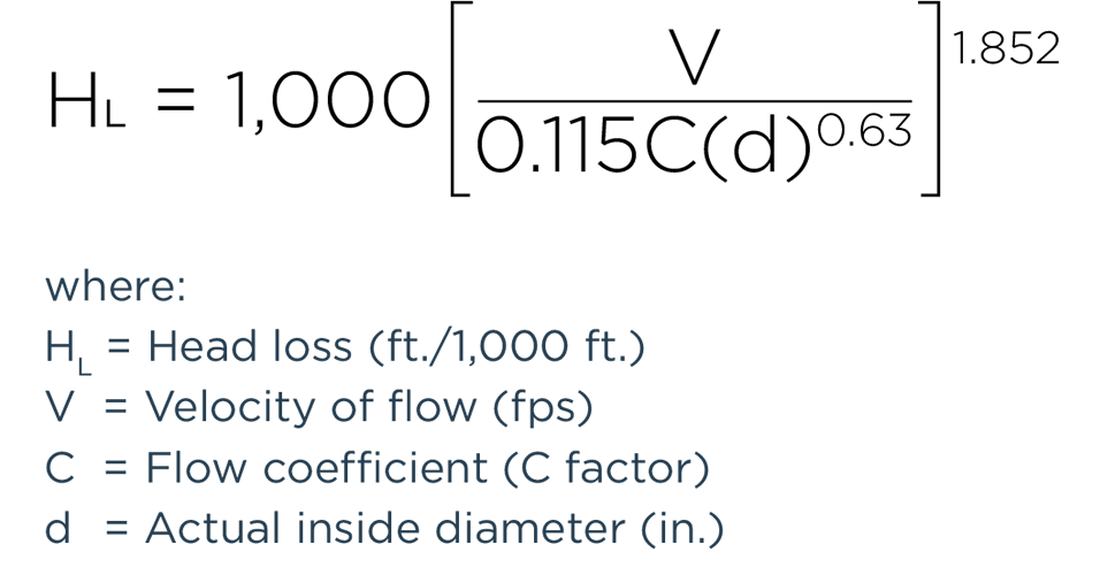
The hydraulic advantages of Ductile iron pipe can also be demonstrated by the flow equation listed below. If you have a constant flow with a smaller area, your velocity will be greater. A higher velocity in a pipeline will create more friction and, ultimately, more head loss.

So, what is the practical side of this evaluation for the water utility?
In order to get water to customers at adequate pressure, head losses must be overcome by using pumps. The energy for pumping is a cost to the water utility in the form of their electric bill. The less energy required, the lower the electric bill to the utility.
These annual energy cost savings can easily be calculated using the head loss value and inserting that value into a pumping cost equation such as that used in the University of Michigan Study, A Framework to Evaluate the Life Cycle Costs and Environmental Impacts of Water Pipelines. (ASCE Conference Proceedings, Pipelines 2016). It can be further extended by evaluating pumping cost savings over many years using a present-worth approach.
All of these calculations can be conveniently performed on the Energy Savings calculator on the McWane Pocket Engineer, where inside diameters of different pipeline materials are evaluated against that of Ductile iron.

Due to its larger inside diameter, Ductile iron outperforms other competing pipe materials regarding flow rates in the pipeline. I mentioned earlier that the roughness on the pipe's interior surface is a factor in calculating head loss. This is commonly known as the “C” factor of the pipe.
It should be noted that some pipe materials have a slightly higher “C” factor. However, running through the head calculations shows this component does not affect pipeline flows nearly to the degree of a larger inside pipe diameter. Furthermore, it has been found by research that the “C” factor of DI pipe remains consistent even throughout many years of service. See the Ductile Iron Pipe Research Association’s report on Cement lining, Cement-Mortar Linings for Ductile Iron Pipe (ctfassets.net).
Now let’s look at an example wherein a utility will install a mile of 8-inch pipeline in a subdivision, a constant pump rate is required due to an adjacent industrial park, and the materials being considered are Ductile iron pipe and PVC (Polyvinyl Chloride). In determining the energy costs to the utility of each respective material, the project model, as noted in the information below, has been established: Please note that the price per kWh will vary per region of the country. Areas with a higher $/kWh will experience higher overall energy savings.
- 8-inch DI pipe vs. 8-inch PVC pipe
- Pipeline Length: 5,280 ft.
- C Factor: 140
- Flow Rate: 695 GPM (Tech Park Demand)
- Unit Power Cost: 0.06 $/kWh (Adjust accordingly per region)
- Pump Rate: 24 hr/day
- Pump Efficiency: 70%
- Design Life: 100 years
- Rate of Return: 5%
- Inflation Rate: 4%
By going through the steps of first determining the respective head loss that must be overcome in each pipeline, then converting that into pumping costs the utility will incur based on the assumptions listed, one finds that using Ductile iron pipe will result in present worth cost savings to the utility of over $80,000 per mile during the 100-year estimated service life of the DI pipe.
Remember, these calculations are just for one mile of pipe. If a utility has two hundred miles of 8-inch pipe within its system, the savings over a 100-year service life jumps to approximately $16,000,000 over the same 100-year service life and assumptions listed above. The reason for this cost savings to the utility is that the 8-inch Ductile iron pipe (Class 350) has approximately 9.76% larger inside diameter compared to 8-inch PVC pipe (DR-14), and this larger area creates less head loss within the pipe.
CALCULATING SAVINGS
The cost savings to a water utility will be more significant when looking at larger diameter pipelines that carry larger flows in a system. Let’s look at an example using 24-inch pipe using the information listed below.
- Length of pipe: 30,000 ft.
- Flow rates: 6,000 gpm
- Unit power cost: $0.10/kwh
- Pump efficiency: 70%
- Pump rate: 24 hrs/day
- Design life: 100 years
- Rate of return: 5%
- Inflation rate of power cost: 3%
Using the previous approach in calculating the energy cost savings to the utility, you find that Ductile iron pipe will result in approximately $1,200,000 present worth of savings over PVC pipe during the pipe’s service life.
Let me clarify that the savings we are talking about in this article represent just the energy savings from lower electrical costs. It does not take into consideration replacement or rehabilitation costs of pipe materials that have a lower service/design life. See the American Water Works Association Report titled, Buried No Longer.
Approximately 85% of a utility’s capital investment is underground. When planning for investment, energy should be an essential component of any municipal system. With rolling electric blackouts becoming increasingly common and the rising population within the U.S. putting higher demands on our energy system, energy savings should be one of the most important items to consider when evaluating pipe materials.
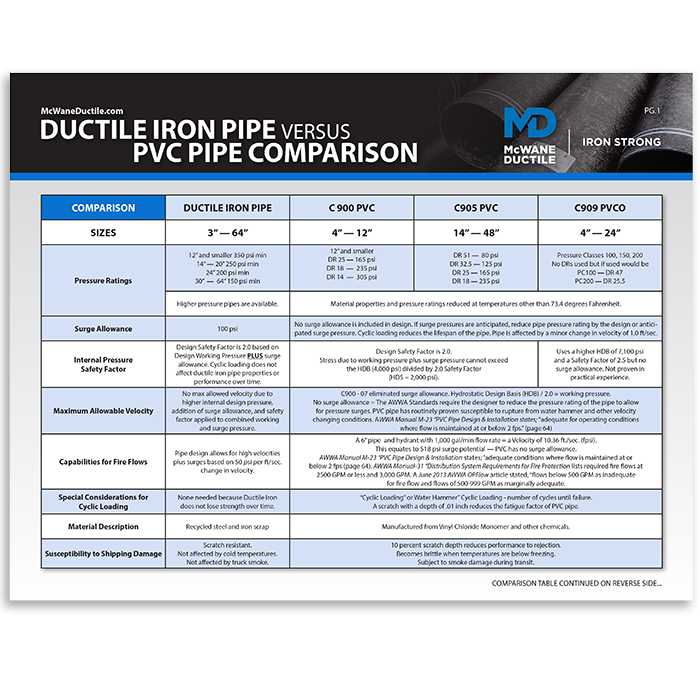
What are the differences and advantages of Ductile iron over PVC pipe? Many things! Use this handy comparison sheet to ensure you specify the safest, durable, and longest-lasting pipe for your next project.
Need Assistance with Your Waterworks Project?
If you have any questions regarding your water or wastewater infrastructure project, be sure to reach out to your local McWane Ductile representative. We have team members who've managed small and large water utility systems, served in engineering consulting firms, and bring decades of experience in solving field issues involving pipeline construction and operation. From design to submittal, to installation, we strive to provide education and assistance to water professionals throughout the water and wastewater industry.