There are many "moving parts," as water professionals know, in the operation of a water system. The intricacies of not only supplying customers with a safe water supply but assuring that supply is adequate, including paramount necessities such as fire protection, many times create an ever-changing balance of key parameters within the water system. When the system operator affects such changes, there should be no concern by the operator regarding the transmission and distribution system to accommodate these changes. This article will highlight two system components that can be directly affected by material selected for system underground infrastructure.
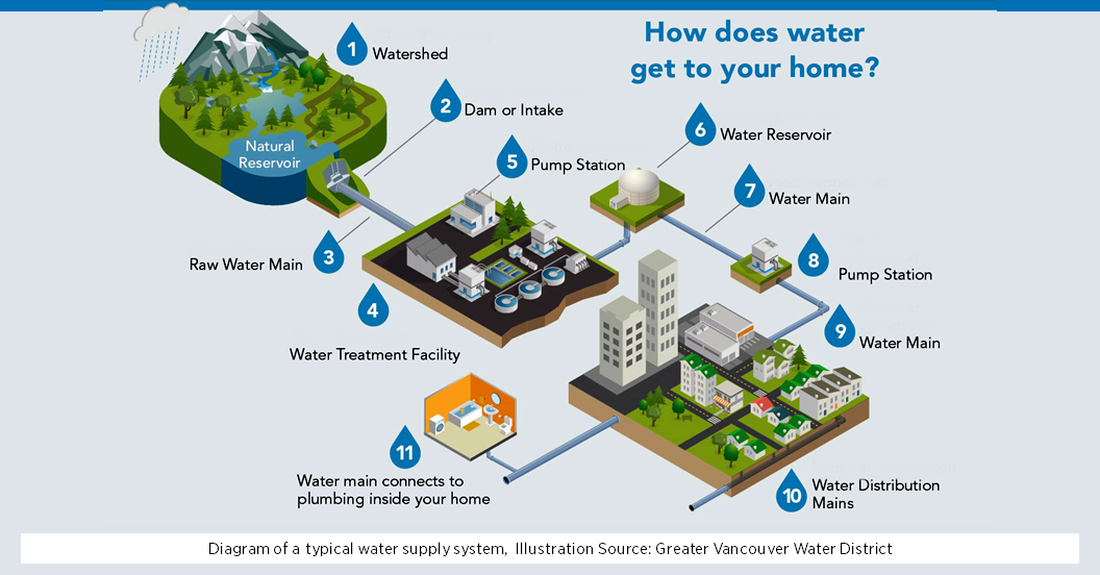
System Gradients
Gradients within a water system are established to provide adequate pressures to customers being served. Every foot of elevation that water rests above a pipeline, .433 psi of pressure is created. Conversely, for every 2.31 feet of elevation, 1 psi is developed. This is primarily done with tanks located throughout the system at specific elevations to accommodate the topography wherein customers are located, although certain ground storage tanks may have pumping units that feed other elevated facilities.
Because storage tanks are costly to construct and maintain, many times, water levels in tanks designed to serve customers at higher elevations can also pose significant pressures for those customers at lower elevations in the same pressure zone.
If pressures on pipelines serving these lower elevation customers are at or near a pipeline's pressure capability, problems can and usually do occur. A change of water velocity in the pipe due to such occurrences as fire flows, for instance, can create what is known as a water hammer if valves are shut down too quickly.
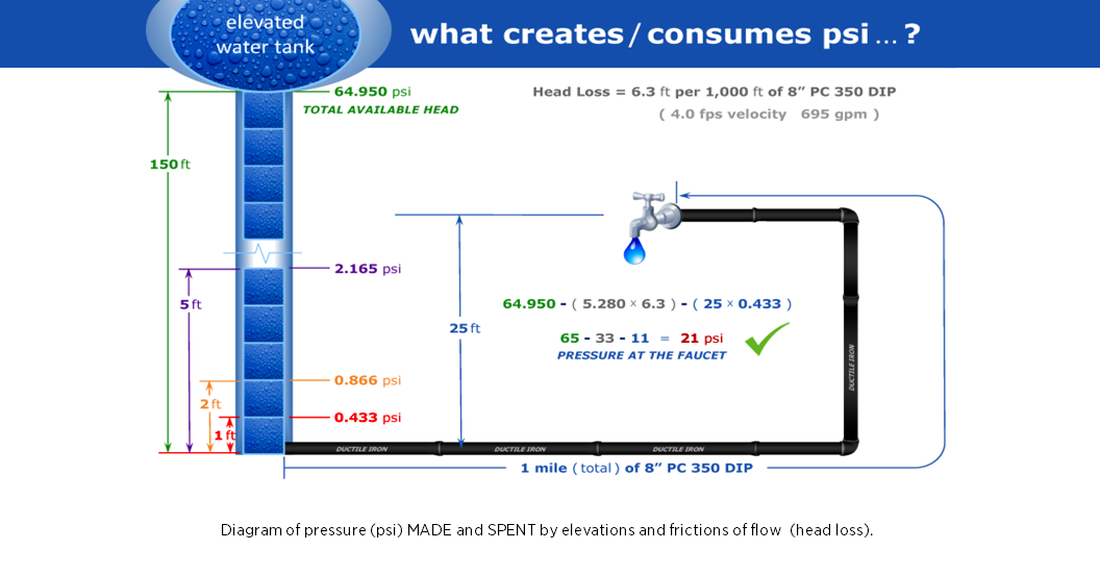
This added pressure which could approximate 50 psi for every change in velocity of 1 foot per second, can easily damage a pipeline if designed only at the threshold limit during normal operations.
Additionally, there are many situations where certain pressure zones are moderated or eliminated for system efficiency. To do so, pressures at lower elevations have been even further increased, thus requiring dependency on the infrastructure there to withstand this operational change.
The use of Ductile iron pipe provides a significant comfort zone for the water system operator under the circumstances just noted. As shown below, provisions to withstand extremely significant pressures, including high operating pressures and water hammer, allows for system flexibility regarding gradient level changes or dramatic pressure changes due to operational issues such as water hammer.

The total design pressure for Pressure Class 250 Ductile Iron pipe would be:
(250 psi “base pressure” +100 psi “surge” ) X 2 = 700 psi “actual gauge pressure”
Similarly, the total design pressure for Pressure Class 300 and 350 would respectively be 800 and 900 psi
(24” Class 52 maximum internal pressure = 1,433 psi) *computed from universal hoop stress equation with nominal wall thickness of 0.44 inches as manufactured.
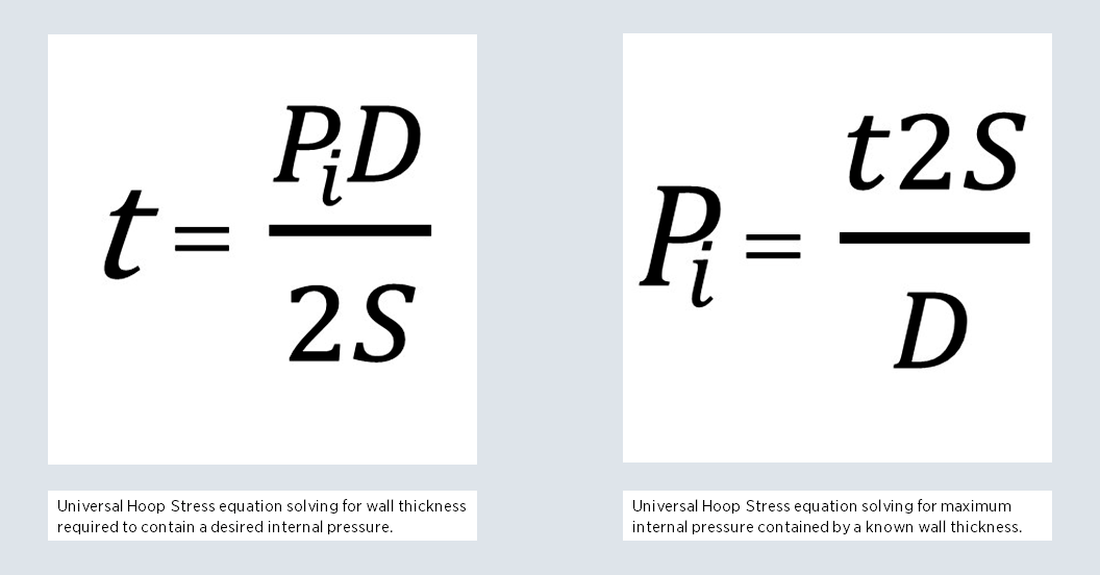
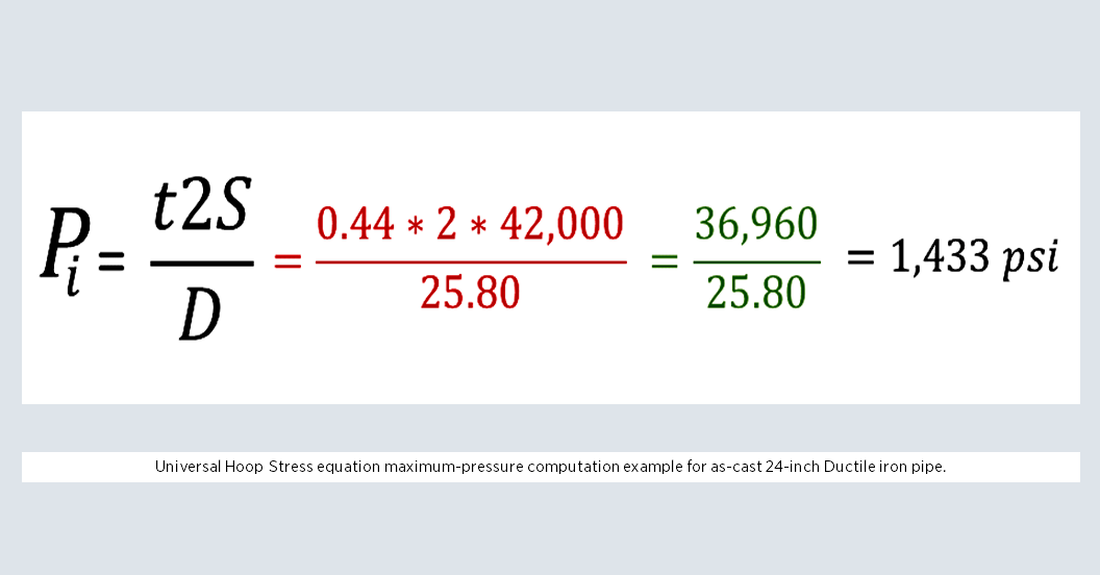
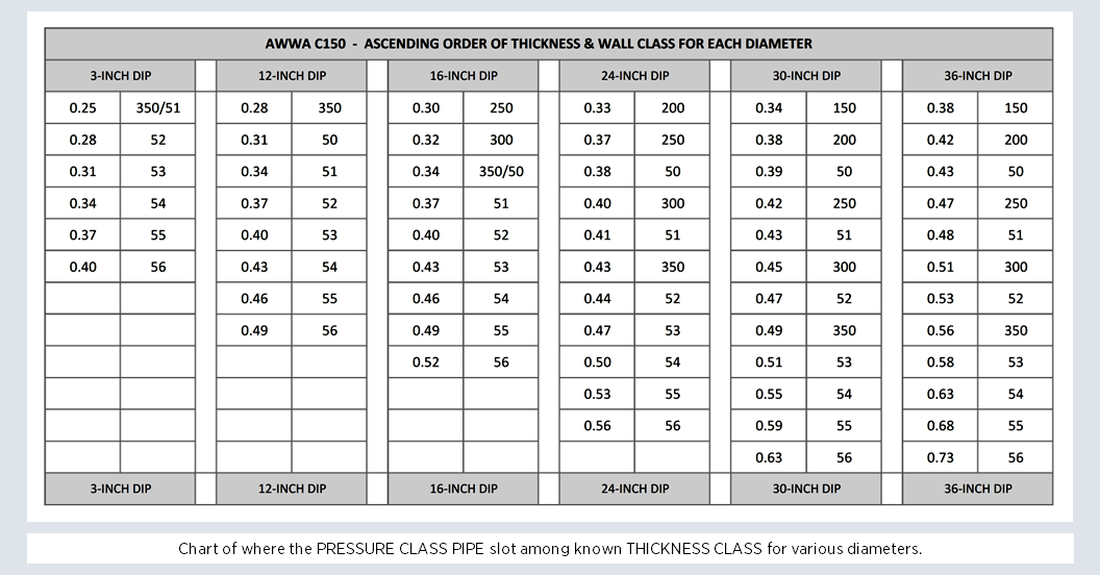
What factor predicts the amount of water required in a system?
When positioned to do so, many water utilities encourage customer growth within their system. Obviously, due to economies of scale, costs of the utility spread over a larger number of customers provide lower water rates to everyone.
Although each water system has different geographical and demographic traits, growth of the system frequently occurs at the extremities where vacant land is available for development. This can entail subdivisions for new homes as well as commercial or industrial growth.
Typically speaking, the flow requirement of customer use is not the governing factor of this new development, although some exceptions can exist with large commercial or industrial customers. FIRE FLOWS needed to protect these facilities generally dictate the amount of water required at system extremities in such cases.
HOW, then, does the proper selection of pipeline material for the underground infrastructure of a utility play an important part in potentially reducing capital costs necessary to serve this new development on the extremities of the water system? I think we are all aware that a larger INSIDE diameter pipeline can carry more water than a smaller one. This is evidenced by the engineering equation:
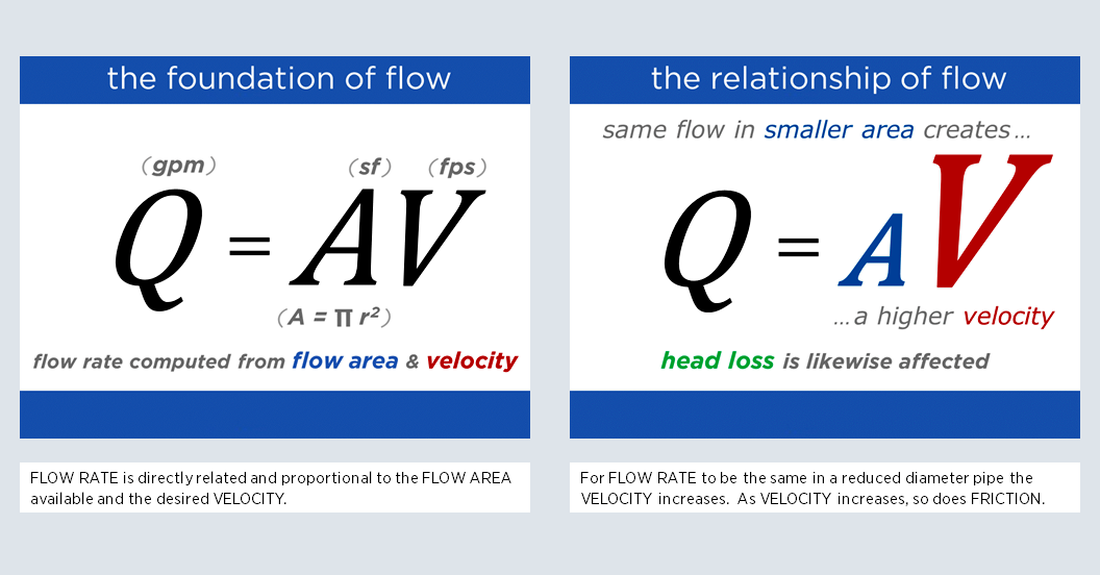
Why is the inside diameter of pipe important?
Because the inside area of the pipeline is directly proportional to the inside diameter of the pipeline, a pipeline with a larger inside diameter will supply a greater flow (Q) when velocities (V) in the pipeline are equal.
Assuming the same velocity of flow, a larger "A," which is a function of the inside diameter of the pipe, supplies more "Q," quantity of water. Now, as a utility continues to install pipelines toward the system extremity, putting in pipes with larger inside diameters will inherently supply more flow per foot installed.
Thus, when a water utility is approached to supply water to a certain location at its system's extremity, most probably with a flow requirement that is linked to fire protection, due to the larger hydraulic (inside) diameters of pipelines installed by the utility, flows on the peripheral of the system will be greater.
Therefore, when new customers locate at those peripheral locations, either required flows are already in place, or reinforcement of the system to obtain the desired flow will be less costly as compared to the need to install parallel pipelines or major booster stations to supplement lower flows resulting from pipelines with smaller inside diameters.
Most water utility professionals are aware of the significant operational advantage when utilizing more hydraulically efficient pipeline material. Because the inside diameter of a pipeline is directly related to head loss experienced in the system, as noted in the Hazen-Williams formula below, overcoming that factor requires energy which can be directly attributed to either lower or higher energy costs to the utility
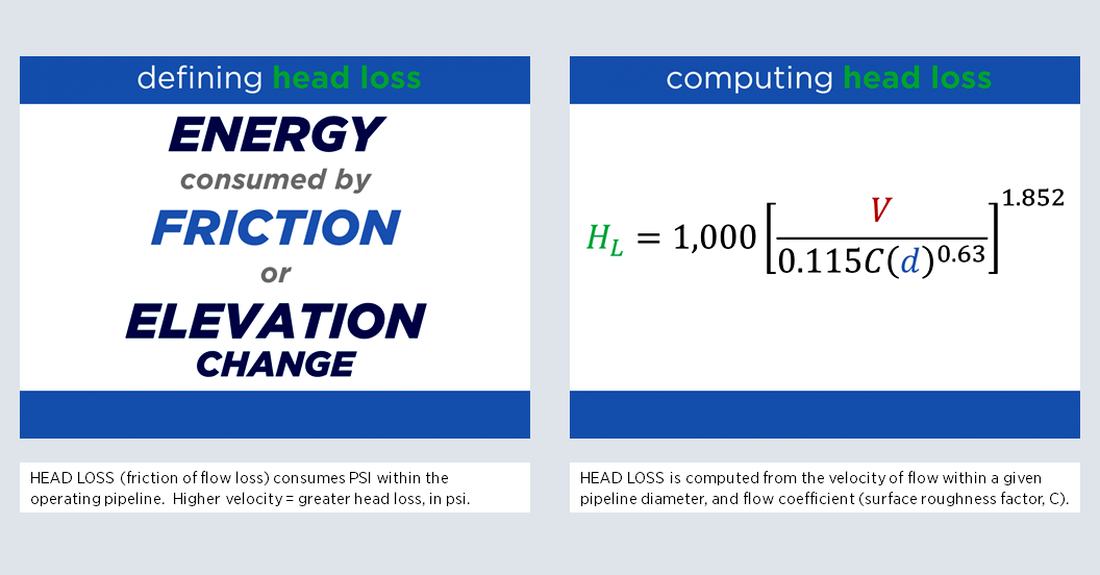
In Summary
We now see through our discussion above capital costs to the utility can also be minimized by installing hydraulically efficient pipelines when growth potential exists on the extremities of the water system. Need assistance identifying key areas for improvement in your current water system? Be sure to reach out to your local McWane Ductile representative. We have team members who've managed small and large water utility systems, served in engineering consulting firms, and bring decades of experience in solving field issues involving pipeline construction and operation. From design to submittal, to installation, we strive to provide education and assistance to water professionals throughout the water and wastewater industry.