Why Are the AWWA Standards Important to Ductile Iron Pipe?
Have you ever wondered what’s behind the AWWA standards? What do they mean? And why do we need them? They’re listed all the time in specifications, mysterious numbers on plans. Have you ever reviewed them to know why they are important for working with Ductile iron pipe (DI pipe)? In this Iron Strong Blog, we will briefly cover some of the applicable standards for DI pipe and how they help you complete your job safely, successfully, and on time.
C150/A21.50-21 Thickness Design of Ductile Iron Pipe
AWWA C150 provides pipeline designers with a recommended design procedure and associated data to use DI pipe with the required wall thickness based on the trench type used, depth of cover, load conditions, internal working pressures, and surge conditions in a particular application or project. Both Thickness Class and Pressure Class pipe are covered under the Standard.
C151/A21.51-17 Ductile Iron Pipe, Centrifugally Cast
Centrifugal casting, also known as the deLavaud process, has been the preferred iron pipe casting method since its invention in 1921. First issued in 1965 and revised nine times over subsequent decades, AWWA C151 covers the minimum manufacturing requirements for Ductile iron pipe used in potable water, raw water, wastewater, and reclaimed water applications.
Like all the standards in this blog, C151 is organized into sections such as:
- I.B – History
- 1.2 – Purpose
- 3 – Definitions
This makes citing the document easy. It continues with "Requirements," in section 4 of C151, which lays out the specifics for manufacturing DI pipe.
- 4.1 – The materials to be used in casting
- 4.2 – The pipe’s ability to withstand harsh or polluted environments
- 4.3 – Standard dimensions and lay lengths
- 4.4 – Coatings and linings to extend the performance life of the pipe
- 4.5 – Acceptable variations for pipe dimensions and thickness
- 4.6 – The requirements for testing pipe thickness
- 4.7 – Manufacturer information must be cast or stamped onto the pipe
Section 5 of AWWA C151, "Verification," details how pipes must be inspected and defines the obligations of manufacturers and purchasers. Testing procedures are explained, and minimum acceptable test values are set. Finally, the section also outlines how test records should be kept and what to do when defective specimens are found.
When it comes to testing procedures, all manufacturers use the same methods, set the same test parameters, and must meet the same minimum requirements. C151 establishes three tests for the quality and durability of DI pipe.
- Hydrostatic Test
- Each pipe is subject to a hydrostatic test of not less than 500 psi. This test may be performed either before or after the coatings have been applied but shall be performed before a cement lining is applied.
- Tensile Test (ASTM E8)
- Ensures that the metal’s physical properties meet the minimum 60,000 psi tensile strength, 42,000 psi yield strength, and 10% elongation required for durability.
- Charpy Impact Test (ASTM E23)
- The Charpy Test measures the energy needed to fracture a sample of Ductile iron taken from a pipe and then calculates the iron’s ability to resist damage from an impact. The test also reveals the malleable quality of the metal sample. Sampels are tested at two temperatures: 70°F +- 10°F / 21 °C +- 6°C for a minimum result of 7 ft-lb or –40°F +- 2°F / -40°C +- 1°C with a minimum of 3 ft-lb.
You can find charts for wall thickness in the C151 Standard, but by using the McWane Pocket Engineer Thickness Calculator, this data is readily available and easy to use.
C104/A C 21.4.16 Cement-Mortar Lining for Ductile Iron Pipe
AWWA C104 focuses on the interior lining of DI pipe with cement to prevent tuberculation. Tuberculation is when chemical reactions between metallic pipe and bacteria found in a pipeline’s water cause the build-up of iron oxide deposits. This Standard is most significant to the manufacture of DI pipe.
Still, it also provides owners and installers with information about the features and specs of the pipe they are working with. There are several factors considered with cement-mortar lining DI pipe, including:
* Cement Type – Types of cement used are typically Portland Type I/II, Type V or Type IL*. The document also lays out the specific qualities of the sand, water, and mortar to be used in the cement.
* Method of Lining – Pipe and fittings are lined using various methods, including centrifugal, projection, and hand application. McWane Ductile provides a video of the centrifugal process for cement lining DI pipe on our Iron Strong blog and YouTube channel. Check it out below.
* Thickness – Per C104, Standard cement lining shall be a minimum of 1/16" for 3"-12" sizes, 3/32" for 14"-24", and 30" and above should have a minimum thickness of 1/8". (Chart available in the actual Standard) Double Cement line requirements are simply the minimum thickness per size of pipe, doubled.
* Lining Quality – Some cracking or crazing is not uncommon in the cement lining. Examples have shown that these issues will repair themselves with “continuous exposure to water because of swelling of the mortar and then will subsequently heal,” also known as autogenous healing. Also important, the Standard establishes the proper materials and methods for repairing defective or damaged areas of cement lining.
* Seal Coat (Curing) – Cement lining can be with or without sealcoat per specifications. For cement lining without sealcoat, special attention to curing is made.
C105/A21.18 Polyethylene Encasement for Ductile Iron Pipe
AWWA C105 covers the use of polyethylene encasement for corrosion protection of Ductile iron pipe. Polyethylene encasement is the most popular, economical, and successful method of corrosion control for Ductile Iron Pipe. Since its first installation in a water system in 1958, it has been used to protect countless miles of cast and Ductile Iron Pipe in aggressive environments.
And now, with advancements in the industry with products such as V-Bio® Enhanced Polyethylene Encasement, the result is a layer that addresses, specifically, the potential influence of anaerobic bacteria and inhibits the formation of corrosion cells under the wrap.
The standards include not only what polyethylene encasement looks like but also detailed instructions on how to install and repair it and precisely how to survey soil conditions at a worksite. C105 notes, “corrosivity with respect to Ductile-iron pipe results from experience with this material in the area under investigation. Every effort should be made to acquire this data.”
C111/A21.11.17 Rubber-Gasket Joints for Ductile Iron Pressure Pipe
Rubber gaskets for pipe joints are the subject of AWWA C111. Gaskets are placed between pipe segments at the joint and compressed, making a water-tight seal. In the 17th century, all cast iron pipe connections were flanged.
The “Push-on” joint was developed in 1956. It improves pipe joint seal, offers greater deflection, and is fast and relatively easy to install. In addition to the specs of a standard gasket, the document also provides valuable advice on how they are installed in mechanical, push-on, and flanged joints.
C600-17 Installation of Ductile Iron Mains and Their Appurtenances
AWWA C600 is a guide for installing Ductile iron pipe into existing distribution systems and for preparing documents for developing new systems or extensions
While extensively detailed, the Standard does not cover unusual situations like piping through walls or unstable ground. A few topics in the Standard are:
- work site prep
- digging trenches
- pipe cutting and joining
- correct deflection procedures
- preventing corrosion
- backfill
- testing new systems
A detailed description of the process and minimum results for hydrostatic testing is also provided. This test confirms the water tightness of the new line and considers correct allowances for movement in pipes under pressure. McWane Ductile has a video on hydrostatic testing on our YouTube channel or view it below.
The AWWA Standard Review Process
There have been many product advancements throughout the rich history of Ductile iron pipe. To keep in step with these changes, each AWWA Standard is reviewed every five years by the A21 committee of the governing body. Comprised of three member categories: General Interest (Engineers, Retired Members, Others), Producers (Manufacturers), and Users (Utilities and Municipalities), all stakeholders are represented in the review. Following the review process, all members must approve the new Standard before it becomes official.
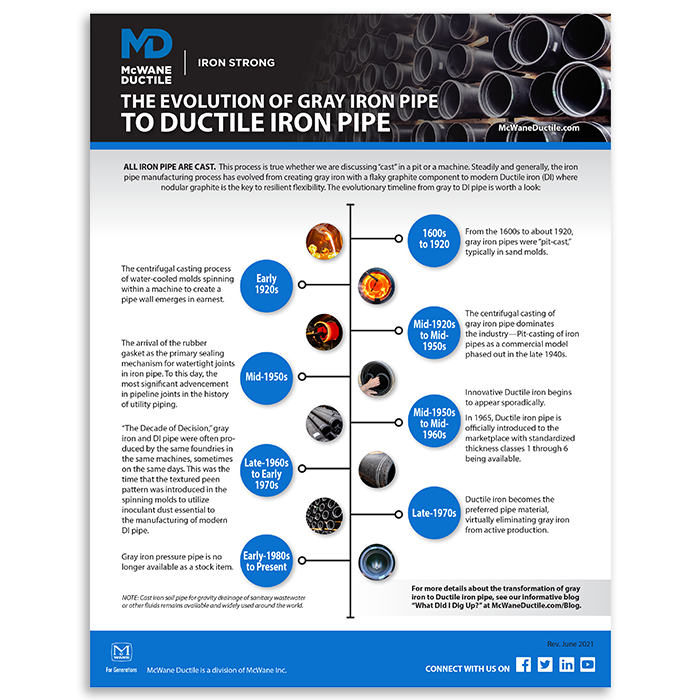
When did Grey iron pipe evolve to Ductile iron pipe? Download this free and helpful timeline tip sheet from McWane Ductile!
Conclusion
These standards are used to ensure a high-quality, uniform product across all manufacturers. Following these standards, designers and installers will be on the same page. They will know what to expect from their systems and the components within those systems. McWane Ductile is proud to be an AWWA member and employ the AWWA Standards when manufacturing quality water products used to build #IronStrong utilities for generations.
Need Assistance with Your Waterworks Project?
If you have any questions regarding your water or wastewater infrastructure project, be sure to reach out to your local McWane Ductile representative. We have team members who've managed small and large water utility systems, served in engineering consulting firms, and bring decades of experience in solving field issues involving pipeline construction and operation. From design to submittal, to installation, we strive to provide education and assistance to water professionals throughout the water and wastewater industry.
*This article has been updated to to reflect the most recent updates to the AWWA C104 standard including the use of Type IL cement in DI pipe.